Full flexibility, Nothing less than this was the goal of Dr. Volker Franke
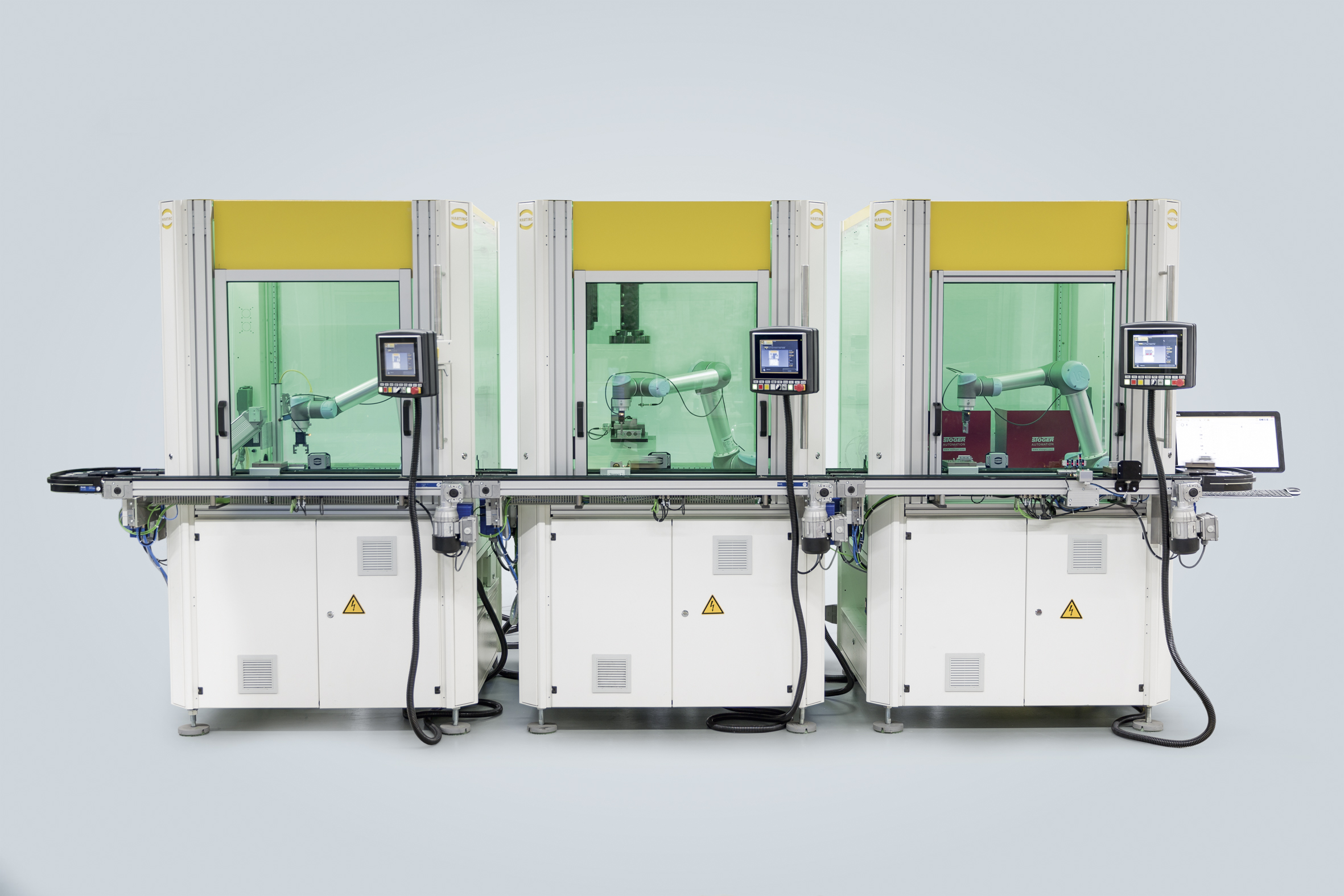
Full flexibility. Nothing less than this was the goal of Dr. Volker Franke when he launched the first innovation project for HARTING Applied Technologies, a subsidiary of the HARTING Technology Group, in the Leading-Edge Cluster it’s OWL 2012.
The project: To redesign the construction of machine plants. The second project followed two years later. This resulted in HARTING’s own Smart Factory. Since then, the company has been thinking in terms of batch size 1 and above. Products are manufactured individually and fully automatically. Plants control themselves.
One click and the connector is configured and ordered. From then on, processing in SAP and production in manufacturing modules at HARTING is fully automated. The system is based on the findings of it’s OWL innovation projects ‘Flexible assembly using self-optimising components’ (Fleximon) and ‘Flexible assembly with integrated interactive robotics’ (Fleximir), which were launched in 2012 and 2014. Outdated technology? No chance.
“We still use Fleximon technology to control our equipment in our new model factory,” says Dr. Volker Franke, Managing Director of HARTING Applied Technologies. Since 2018, this factory has been mapping precisely this individual production. The factory is currently in the implementation phase, says Franke. Since 2016 the technology has been integrated into HARTING’s Smart Factory ‘HARTING Integrated Industry 4 You’ (HAII4YOU). The success story begins earlier than that: The idea of building these self-controlling plants will gain momentum with the first project start in 2012. HARTING will be showing the interplay of several autonomous production islands under the red it’s OWL banner for the first time at HANNOVER MESSE in 2014. In terms of project management, the trade fair establishes itself as a milestone. “We wanted to present something new every year,” says Franke. “And we succeeded“.
But what exactly is behind the flexible assembly concept? In cooperation with the Research Institute for Cognition and Robotics (Cor-Lab), HARTING is pursuing the development of flexible production modules with coordinated hardware and software architecture until the end of the project in 2017. The modules are screwed, assembled and tested. “It is important that the individual manufacturing components in the modules are also autonomous,” says Franke. Another plan is to use ‘plug-and-produce’ capabilities so that the modules can be efficiently reused in different production lines without compromising quality and process reliability.
The HARTING production modules can be dynamically combined without the need for manual programming on site. Thanks to open hardware and software standards, the flexible manufacturing modules can be integrated horizontally into production lines as well as vertically into the company IT. Added to this is an invariant basic structure, which allows the modules to be specialised on the hardware side by means of further process components such as a stamping press.
Both the customer and the company benefit from this flexibility. ” Because of more and more individual customer wishes, we need a versatile production,” says Franke. After all, he says, there is either the possibility of having the products in demand in a large stock on hand or to rely on flexibility and manufacture the products individually within the shortest possible time. HARTING has taken the path from catalogue items to individual solutions. There are fewer and fewer limits to production. Over the years, the initial assembly of the retaining frame for connectors has developed into the automatic production of individual series products. Everything made to specification.
“We have achieved exactly what we wanted to achieve in the projects,” says Franke. However, new challenges await HARTING. After all, networking and automation of the production line generates immense amounts of data. And it is precisely this data that will be the focus of the Technology Group in the future. “The idea of flexibilisation is receding into the background to a certain extent. Instead, we have to ask ourselves what we are going to do with the huge amounts of data and what data we need,” says Franke. The main thing is to draw conclusions from the data as to what needs to be changed when networking the system in order to increase productivity.
About the Leading-Edge Cluster it’s OWL
In the technology network it’s OWL – Intelligent Technical Systems OstWestfalenLippe, more than 200 companies, research institutes and organisations develop solutions for intelligent products and production processes. With support of the State of North Rhine-Westphalia, projects worth EUR 100 million will be implemented between 2018 and 2023. The focus topics are artificial intelligence, digital platforms, digital twins and work 4.0. Named as one of the Leading-Edge Clusters by the Federal Ministry of Education and Research, it’s OWL is considered to be one of the largest Industrie 4.0 initiatives for SMEs. Over the last seven years, it’s OWL has established itself as a driver for competitiveness of the manufacturing industry in OstWestfalenLippe.