Order from Chinese automotive supplier confirms continuing trend towards lightweight technology advanced by Schuler.
In 1993, Schuler delivered the first three hot stamping lines to automobile manufacturer Ford in the USA. What was a brand-new method at the time has since established itself on the market as a global forming technology for automotive lightweight construction – and the trend continues unabated: Schuler has now sold what is the 100th hot stamping line to a Chinese automotive supplier.
“Compared with forming aluminum, carbon fiber-reinforced plastics and dual phase steels, this technology is an inexpensive alternative for lightweight automobile construction,” as Daniel Huber explained, the head of Division Hydraulic at Schuler. Oemer Akyazici, the CEO of Schuler China, added: “Chinese automobile manufacturers and automotive suppliers, such as Shanghai Superior Die Technology Co. (SSDT) or Baowei are increasingly turning to hot stamping.”
The method, which involves heating sheet steel blanks to 930 degrees and cooling them during forming, was first introduced in the early 1990s – initially to improve passenger safety in vehicles – for example, to reinforce the doors in the Saab 9000, thus helping it to pass the stricter crash tests in
the USA.
The technology was first introduced to large series production of the Ford Sierra in Europe and the Ford Mercury in the USA. The side impact beams and bumpers were created on Schuler systems at the time. After the turn of the millennium, the industry increasingly saw this method’s potential for reducing vehicle weight while keeping pace with increasing safety requirements. Because press hardened components have a greater tensile strength than cold-formed high-strength steels, the use of material can be reduced, thus making the components lighter.
In 2006, the body of the Volkswagen Passat was the first to use twelve press hardened components. To allow this to happen, Schuler had built six hot stamping lines within the shortest possible time, and installed these at the Kassel plant. “This laid the foundation for growth that is still continuing,” said Daniel Huber, general manager of the Schuler site in Waghäusel, Germany.
Currently, some 500 million hot stamped parts are produced annually on more than 400 systems worldwide. And, according to Huber, experts anticipate further growth: “Schuler identified this development at an early stage, and set up a Competence Center for press hardening at our Waghäusel site in the year 2006”. This was followed in 2016 by the Hot Stamping TechCenter in Göppingen, a research and demonstration facility at the company’s headquarters.
: Hot Stamping has established itself on the market as an economical technology for lightweight automobile construction.
: In 2016, Schuler opened the Hot Stamping TechCenter in Göppingen, a research and demonstration facility at the company’s headquarters.
: The method involves heating sheet steel blanks to 930 degrees and cooling them during forming. The effect: excellent tensile strength.
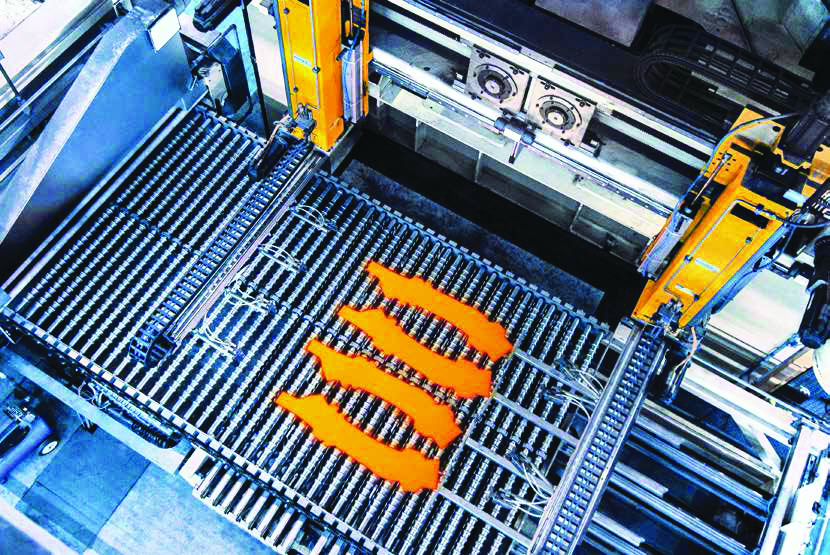
“Chinese automobile manufacturers and automotive suppliers, such as Shanghai Superior Die Technology Co. (SSDT) or Baowei are increasingly turning to hot stamping.”
Oemer Akyazici,
CEO,
Schuler China