Additive manufacturing (AM) has long been heralded for its flexibility as a production method. More recently, AM’s ability to safeguard against global supply chain challenges has helped accelerate the adoption of the technology. Its versatility has made it a leading technology for many manufacturers. In addition, AM possesses unique benefits that are complementary to sustainability and automation, which are increasingly important to manufacturers as they look to build the factory of the future.
Creating sustainable practices
Industrial organizations are beginning to further utilize additive manufacturing to achieve their environmental goals. Several additive manufacturing organizations have joined the Additive Manufacturer Green Trade Association (AMGTA), a global trade organization created to promote the environmental benefits of AM. According to a Forrester report, companies worldwide will only increase their focus on sustainability moving forward and find ways to optimize their manufacturing processes by reducing energy consumption and waste.
Stricter European regulation and U.S. legislation are driving companies to focus on environmentally friendly production methodology. For instance, rail companies in Europe, such as Deutsche Bahn in Germany and Angel Trains in the UK, are printing spare parts directly at sites where they are needed. AM allows these goods to be produced on-demand, on-site, and at scale, eliminating the bulk of carbon emissions from transportation and delivery models. As we grow the scale of these applications, they could have an even bigger impact on reducing emissions in the manufacturing sector.
Furthermore, there is very little waste associated with this additive. Compared to subtractive manufacturing, such as CNC machining, where materials are cut away and disposed of, additive manufacturing can reduce waste and materials costs by nearly 90% while also improving energy use by 25 to 50%. These benefits extend to the related supply chains; additive manufacturing technologies lead to more efficient production paths that help businesses lower their environmental footprints.
Supplementing the supply chain
Additive manufacturing also helps deliver end products to users swiftly and more efficiently, which is paramount amid growing concerns globally surrounding supply chain resiliency. The recent coronavirus pandemic highlighted these vulnerabilities, sometimes with deleterious results. COVID-19 exposed the weaknesses of manufacturing companies with limited flexibility that were highly dependent on excessively optimized traditional manufacturing setups. For example, almost 75% of supply chain executives reported significant supply chain disruptions in 2020 due to COVID-19, with nearly half reporting they did not have sufficient contingency plans in place to deal with such a disruption.
Integrating 3D printing into manufacturing operations can add flexibility to potential supply chain delays by increasing localized production. For example, using digital files, designs can be iterated upon as often or quickly as needed, at little to no additional cost. With a single file source producing various parts, businesses that use 3D printing contract manufacturers have less risk, more control, and added agility concerning their product lifecycle. Local facilities can print designs on-demand from files sent across the globe or print securely from a nearby supplier. In this way, on-demand 3D printing reduces the amount of capital tied up in work-in-progress and finished goods inventories, enabling manufacturing agility. This is one area in which 3D printing is actually “subtractive,” significantly reducing logistics and warehousing footprints.
Automating design innovation
There is an opportunity for design innovation thanks to the unique synergies of additive manufacturing and automation. For instance, Lockheed Martin tapped MakerBot to help develop a fully autonomous lunar rover for NASA’s Artemis program to amplify exploration on the moon. 3D printing has helped NASA engineers design, develop, and test autonomous systems and processes much quicker than they could otherwise by rapidly iterating on designs for prototypes at costs 10x lower than were possible through traditional processes.
Moreover, the synergies between automation and 3D printing flow both ways. AM and automation are driving the factory of the future – aka the smart factory – to support Industry 4.0 transformation. This involves the technical integration of cyber-physical systems into manufacturing and logistics and Internet-of-Things and digital services in industrial processes. By inventing machines that automate processes to mitigate human-centric error, businesses and factory floor staff can track and analyze the unexpected and minimize mistakes. In turn, smart data collection accrued through automation allows businesses to improve their processes, scale-up production, and ultimately make better products. Companies embracing Industry 4.0 concepts of automation, on-demand manufacturing, and part customization to scale additive manufacturing into production require smart, connected 3D printing solutions integrated with their smart factory infrastructure.
We are at an inflection point for global manufacturing – a point in which the burgeoning pressures to upgrade unresponsive supply chains and 20th-century energy-intensive manufacturing and transportation processes are intersecting with a maturity adoption curve for 3D printing. Over the next year and into the coming decade, we will see tremendous growth in the use of 3D printing to reduce environmental impact, ameliorate supply chain issues, and generate resiliency against future shocks. However, we haven’t even scratched the surface in the evolution of the additive manufacturing industry – as AM’s synergies with automation will serve as a transformative technology in the factory of the future.
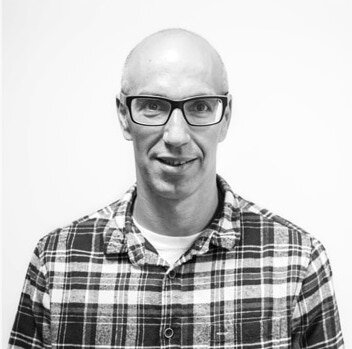
Building the Factory of the Future with Additive Manufacturing
By Nadav Goshen, CEO of MakerBot