Adoption of digital technologies, an important pathway to the fourth industrial revolution, has increased greatly in Indian manufacturing in recent years. Can this pace of adoption be sustained in the new normal? DMI brings together perspectives from industry and academia to provide some clues.
Ravaged by the pandemic, manufacturing companies in India or abroad have found their biggest ally in digitalization of amenable manufacturing processes. Gateway House, an Indian research firm, in its recently published study called ‘Digital Manufacturing in India’ reported that the pandemic has thus compressed long drawn digitization plans from two years to just under a month during the pandemic – with immediate results visible. The study pointed how, industry 4.0 technologies have made it possible for manufacturers to deal with shrunk operating budgets and capital. Sharing the example of Tata Steel and Piramal Glass, it illustrated how managers were able and to operate disparate factory assets by being digitally linked with new generation hardware and software systems at a fraction of the cost.
Technologies typically deployed for digital manufacturing include 3D printing, computer-aided design, data analytics, artificial intelligence, simulation, augmented reality, digital twin technology and sophisticated process management.
This feature presents the perspectives of industry leaders about how – and in what ways – can manufacturers, SMEs as well as large companies, digitalize operations to compete lest they be beaten back by the pandemic and digitally advanced global competitors. We look at the essential components of the trend of digitalization in the Indian manufacturing industry from the perspectives of industry, technology, and skill-building.
India’s Manufacturers: Early Adopters or Early Majority?
On occasion, it’s good to revisit the definition of technology, a term so overused in our times that it’s hard to pinpoint its true meaning anymore. “A technology is a design for instrumental action that reduces the uncertainty in the cause-effect relationships involved in achieving a desired outcome,” said Everett M. “Ev” Rogers (1934- 2004), an eminent American communication theorist and sociologist. Incidentally, Rogers was also the proponent of the Diffusion of Innovation (DOI) Theory. The DOI theory, developed in 1962, has particularly become popular in the last decade as it helped explain the evolution of new technologies (figure 1).
The theory exposited how an idea, behaviour, or a product is accepted by at least 50 percent of the people over time. It explained that a technology, such as digitalization, progresses through its adoption by five types of groups of people. The group that tries the idea first is that of the innovators, people willing to take risks.
The next stage of maturity is when it’s taken up by Early Adopters i.e. people who are not risk takers, but those open to change opportunities. If still ticking, the idea is embraced by the Early Majority, the first sizeable population of the adoption curve, which constituted roughly one-third of the population. The next stage of adoption was that by the Late Majority, the second one-third percentage that is change averse and will only take up an innovation after its acceptance by the early majority.
The last category is that of the Laggards – the conservatives and the traditionalist. From all accounts, when it comes to technology of digitalization, the Indian manufacturing houses sectors that exist on every part of this spectrum. Evidently, sectors like aerospace and defence, pharma, and automotive stand at the forefront of technology adoption, comprising organizations and professionals have become increasingly less risk averse in recent years.
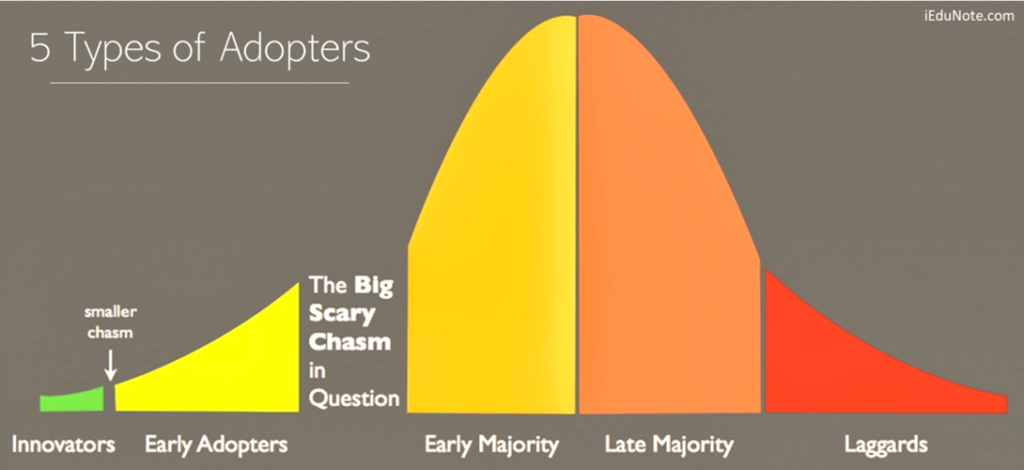
Figure 1: Roger’s Theory of Diffusion of Innovation. Source: www.iedunote.com
It is a growing trend. Suprakash Chaudhuri, VP and MD India, Siemens Digital Industries Software (SDIS) says that Indian manufacturers are beginning to shed their risk averseness and gaining confidence to compete globally, seeking new business avenues and building new business models to keep pace with the market.
The main drivers of this change are industry-centric, he adds. For example, Automotive OEMs and suppliers are devising digitally driven process-planning and execution strategies to deliver diverse products without adding cost.
At the same time, industrial and infrastructure machinery manufacturers are remodelling their businesses to cater to engineered-to-order deliverables. They are enabling their back-end engineering with digital strategies.

Operating at the leading edge of technology adoption, Indian aerospace and defence manufacturers are beefing up their design and engineering infrastructure with simulation capabilities to deliver indigenous, complex systems in a way that they should be able to deliver them right the first time.
On their part, Consumer goods manufacturers are seeking operational improvements through digital systems to balance diverse products formulations and automated manufacturing through transparency and traceability.
Examples of digital technologies being green lit at these organizations include IIOT (Industrial Internet of Things), AR/VR, and predictive maintenance among others. Digital twin, an Industry 4.0 technology, has particularly found favour with companies operating in advanced sectors such as aerospace, precision engineering, and medical equipment. A digital twin is a virtual representation of an object or system that spans its lifecycle, is updated from real-time data, and uses simulation, machine learning and reasoning to help decision-making.
A recent study highlights that the current digital twin business market of 5.1 billion dollars in 2020 is estimated to reach 115.1 billion dollars by 2035. Sameer Jindal, Director Engineering, MG Motor India says that digital twins, which is one of the critical tools in realization of smart cities, is powered by latest technologies such as Internet of Things (IoT) and Artificial Intelligence (AI). Enabling digital twins facilitates in automating many services and assists in unforeseen situations such as disaster management and mitigate pandemic spread, he adds.
The pandemic has made the role of digital twin one of paramount importance.
“The application of digital twins in pandemics is even more vital as its use not only results in cost reduction, performance enhancement, and convenience at various levels but also reduces the risk of spreading disease,” says Mr. Jindal
The automotive technology has been among the biggest users of digital technologies. Highlighting some instances of digital adoption, Mr. Jindal cites the installation of sensors in the Brake Pads that has helped with predictive maintenance as well provide information to engineers to design systems that could help reduce errors made by drivers.
An excellent example of the use of Data Analytics in automotive is the concept of Car As A Platform (CAAP), says Mr. Jindal. Customers are increasingly using CAAP to make a host of decisions ranging from ordering grocery and pizza to booking their space at EV charging stations before reaching the place.
Customer experience is, in fact, of the areas that have benefited the most from digital technologies. VR/AR, for example, is becoming a popular choice for companies in offering a digital experience of the product to the consumers, Mr. Jindal adds. Some other prominent examples of digital transformation put to use for customer experience include the partnership of the Bengaluru-based 3D AI firm Avataar.me with MG Motor India for the automotive company’s new product line-up for the creation of life-sized AR compliant renders on Facebook and Instagram platforms, using Avataar’s AI platform. “The experiences were brought to life in partnership with Facebook & Instagram during the 2020 Auto Expo,” Mr. Jindal shared. Incidentally, Honda Cars launched their virtual showroom recently. The showroom allows customers to interact with the digital version of a car.
Digitalization’s Goals
As industries move past the phase of frenzied adoption of the pandemic years, the industry will have to decide the mid- and long-term priorities of digitalization. Iconic brands such as Apple, Samsung, and Maruti Suzuki and even the new trailblazers are demonstrating that a sharp focus on customer needs provides manufacturers the right set of priorities.
The topmost digitalization priority for Indian manufacturers today needs to be data acquisition and deriving insights which helps with effective decision making, says Mr. Chaudhuri. The next set of priorities that drive digital initiatives must be efficiency improvement and error-free production. Initiatives such as process plan simulation, automation validation, real-time scheduling, and integrated quality management help with this goal.
For manufacturers whose value chain starts from R&D, digitalization priority must be that of enabling design automation and performance simulation focusing on delivering products as per customer specifications.
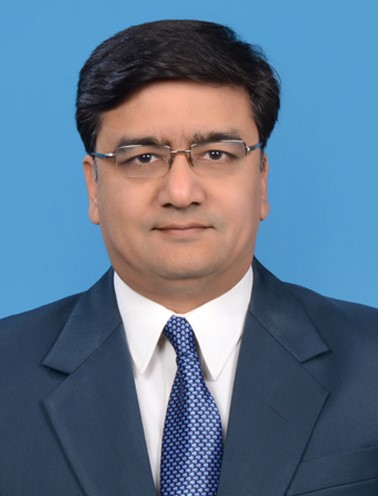
Globally, the biggest impact of adoption of digital technologies is seen in the SME segment. In India, the SME segment is evidently reluctant to embrace advanced management practices including those that require digitalization (Savitskie et al., 2022). MSMEs contribute around 6.11 percent of India’s manufacturing GDP and 33.4 percent of the manufacturing output. Even more, they provide employment to around 120 million people and contribute around 45 percent of exports. Enabling this segment to embrace digital technologies could pay sizeable dividends.
Mr. Chaudhuri points out that SMEs in India are lately acknowledging the relevance of digitalization in the emerging market, but, generally speaking, they appear to be hesitant to invest and implement owing to a paucity of funds. He adds, “To make it easy for SMEs to adopt digital technologies, we offer Xccelerator, a comprehensive portfolio of solutions and services that are designed to achieve better results, faster. SMEs can invest when they are needed and adapt and scale from there.”
The engineering software enables innovative product and manufacturing design while robust collaborative framework ensures that up-to-date data is available as and where it is needed, throughout the design, production, and usage stages. In addition, SMEs can make use of cloud-based analytics and low-code application enable data collection and analysis from the factory floor and products in the field, integrating actual usage data back into product development for continuous improvement.
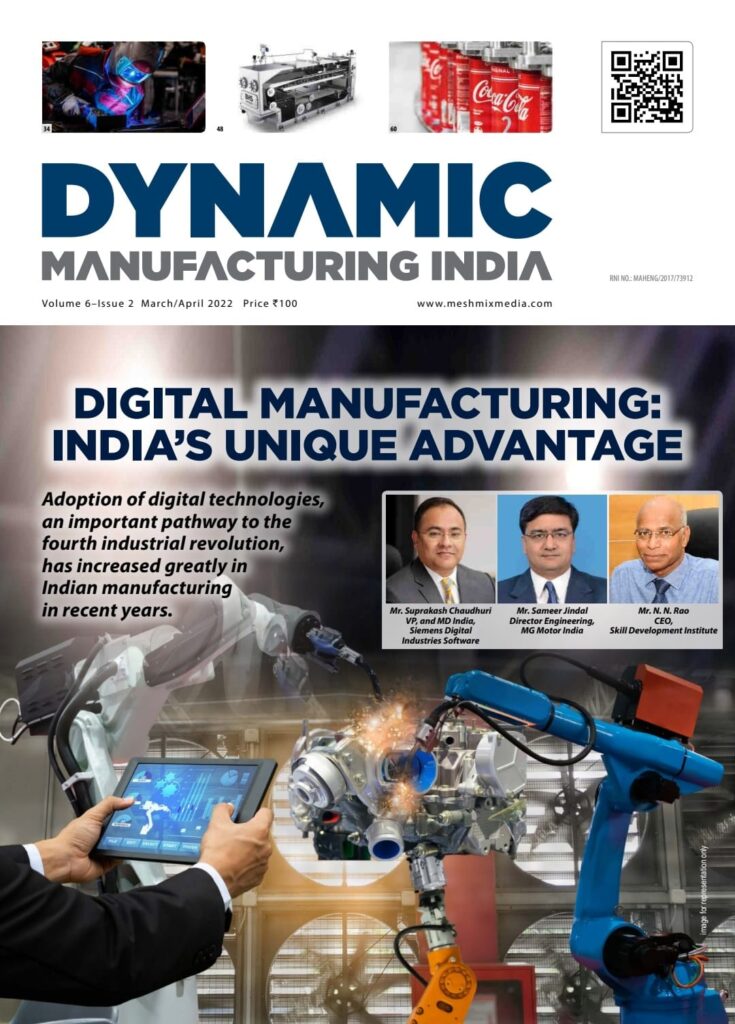
For manufacturing organizations across the board, digital adoption relies on the buy-in of entire organization. Mr. Chaudhuri says that his team’s experience of working with customers in India has shown that it is not just about implementing technologies, the processes around it must be revised and enhanced to utilize the capabilities of the digital technologies. This requires all the stakeholders – leaders, managers, and employees to be aligned to execute, with customer satisfaction as the pivotal objective, he emphasizes. “Therefore, my recommendation would be to create a shared vision through management commitment, capture the current process gaps and document the transformed state of processes. While the implementation could be in baby steps, the transformed value chain needs to be defined holistically and reviewed for progress periodically.”
Empowering Customers
Various surveys have shown that the main hurdles that Indian organizations face with digitalization programs are issues like data security concerns, the lack of a digital knowhow, and a lack of the will to invest. How are the organizations coping with these challenges?
Mr. Jindal concurs that big-data analytics needs be implemented with the appropriate security and privacy measures in place. MG Motor India, has for example, gone for top layer of cyber-data security for the same reason.
The upside is that, with companies moving fast on the road to digital adoption, addressing all the rightful concerns, they can tap into the growing demand for digital features, product customization, specialized after-sales support, and improved supply-chain metrics like a faster time-to-market.
Mr. Jindal echoes the sentiment. There is an increasing demand for digital features in the metros especially among the young population. “The young generation is now getting used to digital data and the usage of applications.” However, there are still large sections of Indian population particularly in the small cities which are unable to take advantage of digital adoption. Data connectivity is still a big issue for cars in these areas, for example.
Nonetheless, digital revolution is changing the customer preferences everywhere. The customers are showing high interest towards digital technologies and features like ADAS (Advanced Driver Assistance Systems), AI-powered and IOT-connected cars. “Further, the pandemic has also brought in the factor of sustainability. It is gaining attention and popularity among customers with a emotion of contribution to the environment and society,” says Mr. Jindal.
The Role of Skill Development
The adoption of digital tech in manufacturing is closely connected to the level of skills of workers and engineers who work with them. India’s workforce, in this aspect, is extremely divergent. On the one hand, we have information technology professionals that are among the most accomplished and sought after in the world. On the other hand, our productivity performance, a measure of our skill level, fares poorly for a large economy. India’s labour productivity and capital productivity levels don’t compare well advanced industrialized economies.
The productivity levels of China and South Korea, for example, measured in GVA output per full-time-equivalent worker, are four times higher. The sector-wise disparities are even greater – South Korea’s electronics manufacturing sector, for instance, is 18 times more productive than India’s. Even more, Indian manufacturers ostensibly operate well below their maximum capacity, with utilization ranging from 60 to 70 percent across sectors, as the Reserve Bank of India figures.
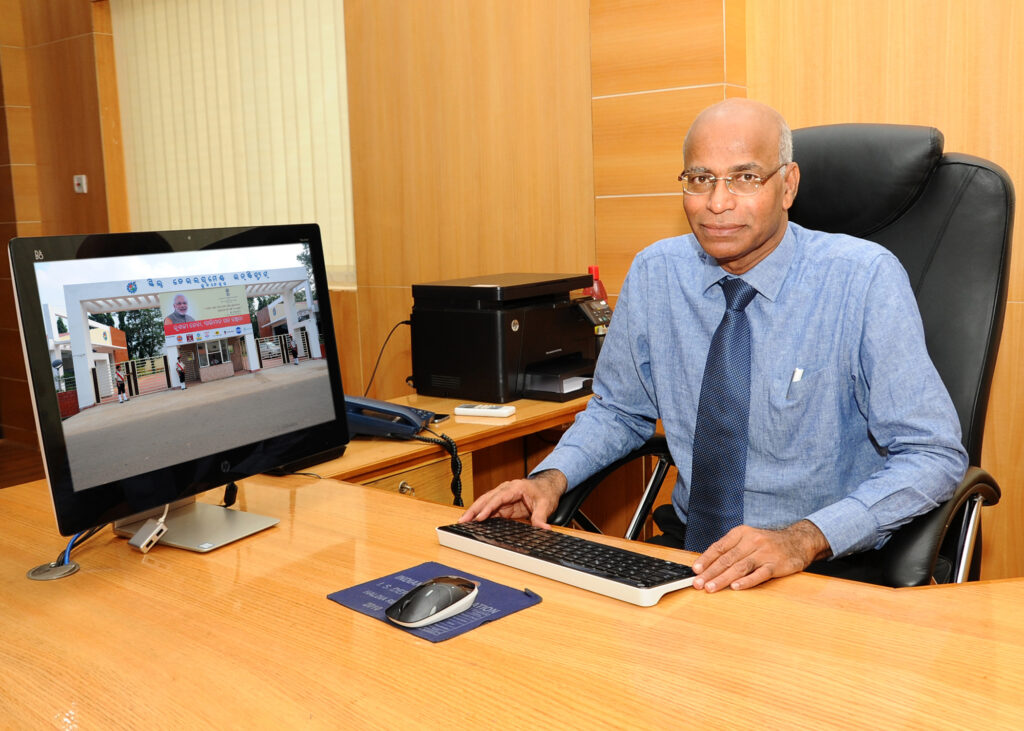
The good news is that Indian organizations realize the importance of this attribute. Mr. Chaudhuri informs us that Siemens Digital Industries Software in India is working with skill building institutes to train the shopfloor resources in digital technologies ranging from design to manufacturing. The training courses are segregated according to the technical trades as required by Indian industries. “Our value-add is in crafting the pedagogy, training the trainers, developing lab experiences to support the training, exposure to industry challenges and ensuring that the trained manpower, on being employed, deliver value in the emerging environment of speed, efficiency, quality, and cost consciousness.”
The role of the academia, particularly the trainers, is of paramount importance in bringing about digital transformation at organizations, including the SMEs. One of the institutes that is doing notable work in this area is Skill Development Institute (SDI), Bhubaneswar. Promoted by Oil PSUs, namely IOCL, ONGC, GAIL, HPCL, BPCL, OIL, EIL and BL & CO, SDI is managed by Indian Oil Corporation Limited under the aegis of Ministry of Petroleum & Natural Gas, in line with Government of India’s Skill India mission (read more about the institute in the box About SDI, Bhubaneswar.)
The institute’s Chief Executive Officer N. N. Rao says that the institute has designed the skill-building courses as the per the industry’s demands. “They cover the diverse functions of industrial infrastructure, product design, product testing, manufacturing planning, shop floor and the allied IT services.” The curriculum of Industrial Infrastructure, for example, includes focused training modules for welding, pipe fitting, fabrication, instrumentation, building & industrial automation, CCTV and building maintenance. Similarly, the product development and manufacturing training course prepares students for efficiencies in areas like CAD/CAE/CAM, process design, Computer-aided Test and Simulation, robotics programming and advanced welding. The institute focuses both on the process and on the outcome. “Essentially, most industry needs can be fulfilled by the trained manpower ready to deliver from day one of their employment. We take care that the resources are not only trained on the technology but also the processes that use the digital technologies to fulfill the industry needs,” emphasizes Mr. Rao.
It is a common experience among industry’s employers that a lot of graduates from engineering colleges and training institutes are not sufficiently suited for real-world handling of functions, particularly those pertaining to digital technologies. “There exists a wide [skill] gap among students coming out of engineering colleges, especially when it comes to their efficiencies with IIOT, ADAS and EV (Electric Vehicle) technologies,” Mr. Jindal says. And in the event of managers not having enough time to train new recruits, the latter have no option but to learn industry-ready skills on the go. “There is a need is to provide a hands-on experience to the students from the college days itself. Colleges and institutes need to tie up with manufacturers for internships and collaboration.” Mr. Jindal points out IIT and some private colleges in states like Gujarat now offer such specialization course such as Masters in Internet and Electric Vehicle projects.
On its part, SDI Bhubaneswar makes imparting industry-ready skills its core priority. Its state-of-the-art infrastructure consisting of course labs and workshops provides both digital and physical modes of delivery for the purpose. “The students get to work on machines and equipment which are being used by the industry. Additionally, SDI has also created a Digital Literacy Lab in which students are provided with an opportunity to improve their digital skills, says Mr. Rao.
As important are the various linkages and collaborative networks that institutes build with the industry. SDI has been proactive on this front, adds Mr. Rao. “SDI Bhubaneswar has formed partnerships with reputed organizations such as Schneider, Siemens, Cisco, Kempii, Lixil, etc. These industry partners bring in advanced curriculum and pedagogy to impart market relevant skills.”
These perspectives from industry and academia therefore portend that the Indian manufacturing sector has the right ecosystem for ushering in digital transformation for all its companies, irrespective of size. The fast-changing needs of today’s customer who has become truly global in her expectation and aspiration, could just provide the right trigger for the transformation.
About SDI, Bhubaneswar
SDI runs Skill Training courses to unemployed and under privileged youth of Odisha in a pilot campus in Mancheswar Industrial Estate, Bhubaneswar. This Institute is providing skill certificate programs on Welding, Electrical, Computer Data Applications, Fitter Fabrication, Instrumentation Technician, LPG mechanics, Pipe fitter – City Gas Distribution & Solar PV Installer ( Suryamitra)– who can be employed readily on the job.
The course curriculum is aligned with National Skills Qualification Framework (NSQF) of Government of India and can also provide customized programs. In addition, the institute also provides assistance and encourages entrepreneurship and self-employment. The full-fledged world-class state-of-art main campus of SDI Bhubaneswar with international standards was formally inaugurated on 24.02.2019 by Hon’ble union Minister Shri Dharmendra Pradhan at Jatni in 46.172 acres of land. The labs are being set-up through industry partners.
The Institute SDI is projected to impart skill development training to over 50,000 students in 25 regular trades pertaining to the hydrocarbon sector and local industry needs, over a period of next few years from inception, apart from other employment-oriented Skill training beyond the petroleum sector in line with National Skill Development Mission of Government of India.
Ready-to-go orientation
To make trainees employment ready, SDI Bhubaneswar believes that, a student should be trained with a 360 degrees perspective. SDI Bhubaneswar, therefore, emphasises on providing employability skills including basic communication and IT literacy to all the candidates apart from the core technical training. SDI Bhubaneswar has tied up with Mahindra Pride for the delivery of life skills to the students to improve their soft aspects. Various tools such as quizzes, assessments, assignments, and short projects have been deployed to assess the skill acquired through the trainings.
SDI Bhubaneswar also offers opportunities to the students to display their talents through sports and extracurricular activities and hone their leadership skills by getting involved in the student committees which assist the operations and the administrative functions of the Institute. At the end of the training, the trainees are assessed by external assessment agency and a joint certification in coordination with the Sector Skills Councils and National Skill Development Corporation is awarded to the students.
Associations with industry
There are several ways in which the industry can associate with us – from alignment to recruitment, through the students’ training lifecycle. The first and foremost step is to believe in the essence of SDI Bhubaneswar and understand our philosophy and vision. All the stakeholders who are interested to associate with SDI Bhubaneswar are first requested to visit the campus and spend a few days to familiarize with the campus, its students, and the environment. We believe in “Seeing is believing”. Post the visit, the stakeholders can evaluate SDI’s value proposition.
The association can be in any of the following avenues:
- Curriculum development/review/inputs
- Advanced equipment and machines for industry aligned training
- Customized courses which include need specific training areas
- Industrial visits, short assignments, and on-site projects/internships
- Guest Lectures, workshops, and other interventions
- Placement opportunities for the students of SDI Bhubaneswar
Please refer to the website www.sdibhubaneswar.in for more information.