Under the motto of ‘Connecting systems for intelligent production’, the exhibitors at EMO Hannover 2017 presented innovations designed to network the world of metalworking and progress its technological optimisation. There was a particular focus on cloud- and offline-based solutions for networking machines, tools, handling aids and production sequences, in order to achieve the intelligent production operations of tomorrow.
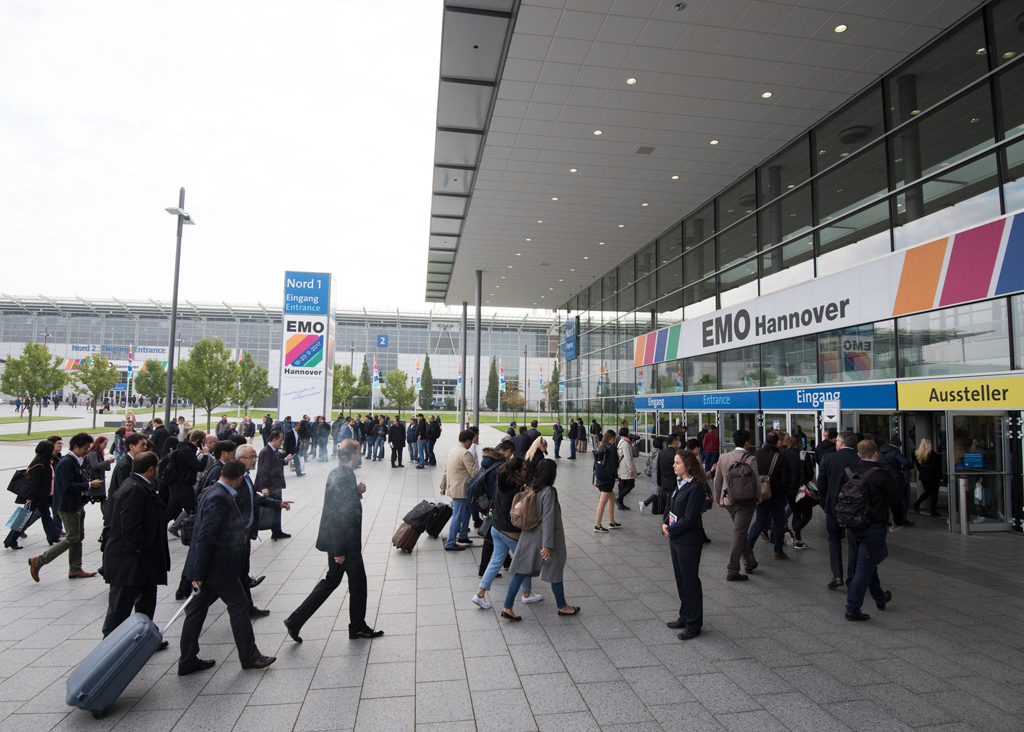
Networked machines, whose operating states can be acquired and statistically evaluated at any time, plus intelligent tools in conjunction with intelligent tool management systems, constitute only one aspect of tomorrow’s manufacturing operations. Improved service structures at the customer’s facility thanks to smartglasses, comprehension-enhancing projections of complex tools using augmented reality, increase the customer benefits involved. But solutions for security-driven management of the data generated were also presented.
From a technological viewpoint, many innovations were spotlighted in the field of additive manufacturing. Besides new machines for producing additive components, numerous exhibitors showcased new process variants, and demonstrated their capabilities as exemplified by innumerable additively manufactured components. The use of innovative materials, such as CFRPs for machine tool spindles, renders processes faster and more productive. Responsively customised tool dimensioning and more efficient machine tools additionally enable significant gains in productivity to be achieved in conventional chip-cutting production of high-precision components.
The descriptions below exemplify what trends and issues are the major focuses of production technology today
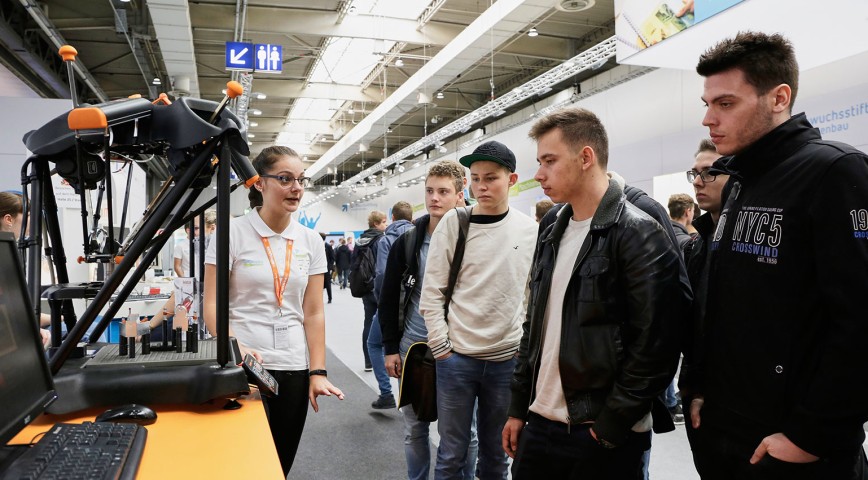
Additive Manufacturing
The proportion of additive manufacturing in the industrial environment continues to increase. This trend was discernible almost everywhere at the EMO Hannover, due not least to the numerous impressive additively manufactured application examples at various stands, with which the exhibitors showcased their hardware and software solutions. Additively manufactured products can not only be manufactured for optimum load-bearing capacity and weight by generatively building up bionic structures, but also permit the integration of additional functions, such as selective internal heat dissipation through integrated cooling channels. For metal printing, two processes currently predominate: the powder-bed process and laser deposition welding. Criteria for creating structures from the powder bed are primarily the high degree of design freedom, and fine resolution with 30 micrometres.
On its stand, EOS from Krailling exhibited an additively manufactured injection head for a rocket engine from the Ariane Group. By using powder-bed-based technology, the construction time could be reduced from three months to 36 hours, the costs halved, and the number of individual parts reduced from 248 to a single component. One issue gaining steadily in perceived importance is quality assurance in generative manufacturing, particularly when it comes to safety-relevant components for aircraft construction. In conjunction with MTU Aero Engines AG, EOS creates solutions that monitor the system’s general status by means of numerous sensors. Optimum layer quality is additionally assured by camera-based surveillance of the exposure process and the melting behaviour of the material.
Besides the powder-bed process, the technology firm Trumpf from Ditzingen showcased at its stand the process of laser deposition welding, which enables build-up rates to be achieved that are ten times higher than the ones obtained in the powder-bed process. Here, the laser creates a melt pool on the component’s surface, into which metallic powder is inserted via a nozzle. This production process is used for applying wear-protection layers, repairing components, and for creating new structures. The Trumpf lasers could be viewed in operation on the multi-tasking machines of the Laser EX series, which the Japanese machine tool manufacturer Okuma was premiering in Europe on the opposite stand.
Consistently harmonised solutions from a single source, from the CAD/CAM software to combined machining of the finished part, were presented by the machine tool manufacturer DMG Mori, Bielefeld. With the new Lasertec SLM, components up to a maximum size of 300 mm x 300 mm x 300 mm can be created from the powder bed. The premiered Lasertec 65 3D even produces components with a diameter of 650 mm and a maximum height of 560 mm in an additive process. This machine, designed purely for additive manufacturing with the powder nozzle, requires 45 per cent less footprint as compared to the hybrid model, and offers not only a 40 per cent larger work space but also technological innovations like different track widths, higher laser ratings of up to 4 kW, and manufacture featuring reactive materials like aluminium and titanium.
Functional layers and component structures are created entirely without lasers using additive 3D coating technology from the machine tool manufacturer JG Weisser Söhne in the Black Forest. Using a patented process, simple semi-finished material is rotationally imprinted onto a component’s surface, melted by the friction this generates, thus converting the semi-finished material into a component. The experimental machine showcased at EMO Hannover offers additive deposition a work space of about 800 mm x 300 mm x 150 mm. However, there would be a potential for utilising the technology on machines with different work spaces, and besides additive deposition combining it with further machining units for mechanical reworking. According to this company, the advantages compared to the laser-based additive manufacturing process featuring a powder bed are that the semi-finished materials are 10 to 30 times more affordable, that the deposition rates of two litres per hour are 20 times higher for aluminium and even up to 100 times higher for steel. One significant disadvantage, however, is that currently no complex structures can be created.
The metal-powder deposition process of Hermle Maschinenbau from Ottobrunn does not require any lasers either. In this thermal injection process, metal powder is accelerated to very high velocities with the aid of a carrier gas and applied layer by layer via a nozzle onto the component’s surface. The advantages of this process are that there are hardly any restrictions on the choice of material, provided that it is available in powdered form, and that it is possible to apply up to seven different materials in any desired mixing ratio on free-form surfaces. Other advantages are the low temperatures of 200°C to 300°C and the good amenability to a combination with subtractive mechanical machining processes, such as milling or turning, in a machining centre.
With the 3DXpert holistic software package, the American company 3D Systems from Rock Hill, South Carolina, offers a complete software package for additive metal manufacturing. This manufacturer, which itself also produces machines in the field of additive manufacturing, thus presented a solution constituting a producer-/process-independent variant for creating additive components. After the data has been imported and the component has been positioned, it is easy to subsequently create and optimise its structures and support geometries for the production operation. Then both the printing strategy for individual segments of the component is defined, and the scanning tracks are calculated. Since after additive manufacturing it will be necessary to rework individual surface areas and remove support geometries, the software also offers a part-step for this step in the process as well.
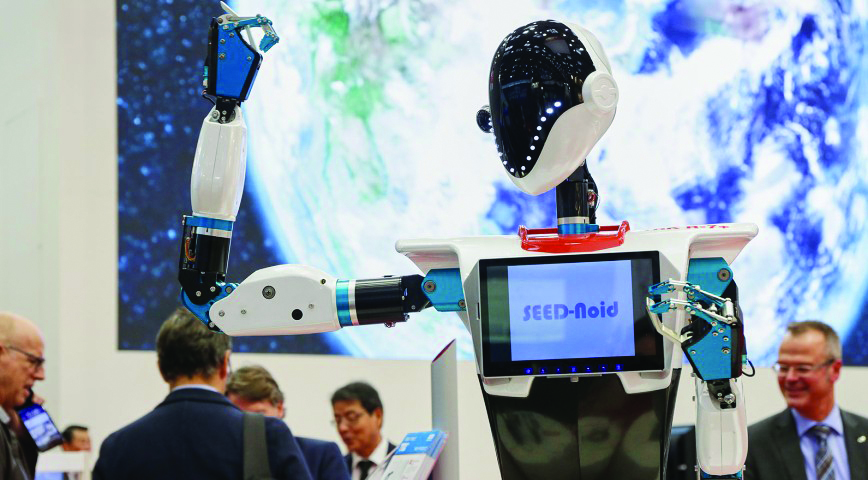
The VDW’s Sectoral Initiative for Networked Production
The VDW (German Machine Tool Builders’ Association) has launched a sectoral initiative for networked production. Its aims are development and software-based implementation of a standard for linking a whole array of highly disparate machine control systems at a shared interface. The initial phase of the project involves a core team comprising not only the VDW, but also prestigious companies like DMG Mori, Emag, Grob, Heller, Liebherr-Verzahntechnik, United Grinding and Trumpf. With this collaboration, unique in its form, between firms from the machine tool industry and the VDW, machine tools are to be prepared for the digital future, and an urgently necessary foundation for ‘Industry 4.0’ created. The planned standard is tasked with making it possible to interchange data between machines with different control systems of many generations and forward them to manufacturing execution systems and/or to the cloud, in order to evaluate the data and utilise them for optimisation tasks. The goal of the initiative thus lies in harmonised networking of the production operation based on secure interfacing with EDP systems and clouds. Initial results are already expected for early 2018.
Intelligent Tools Thanks to Integrated Sensor Technology
The Swedish tool manufacturer Sandvik Coromant from Sandviken exhibited a series of tools as part of its Industry 4.0 initiative. Here, under the roof of Coroplus, integrated sensor technology in tools and tool-holders during machining was spotlighted. For vibration-damped drilling rods, the silent tools, the final machining steps in elaborate components can be monitored using app-based systems. The customer can see whether the tool has engaged and what the thermal stress in the drilling rod is like. The manufacturing process for expensive and complex components is thus monitored. In addition, intelligent tool-holders forward data on running time, loading and battery status to an app and thus incorporate the idea of predictive maintenance. Fine-drilling heads can be precisely adjusted by means of an app for manufacturing accurate borehole diameters. A comparable solution is also offered by BIG Kaiser from the Swiss town of Rümlang. This means the tool does not have to be manually adjusted in the tool pre-setting device, but can, for example, be extended and retracted for different diameters directly in the machine using an app on the tablet. This shortens process chains and reduces non-productive times during tool adjustment
Intelligent Countersink Tools for Interior Component Machining
The high-precision-tool manufacturer Hermann Bilz from the Swabian town of Esslingen has for many years now been producing countersink tools. These are used where the surface to be machined can be reached only through a borehole, e.g. in closed housings. A reversal of the sense of rotation causes the tool’s blade to be extended. In order to remove the tool from the borehole after machining, it is essential to retract the blade. Under the aegis of a joint project with O. Bilz and EWS, the Hermann Bilz company has developed a countersink tool that monitors retraction of the tool blade. The data are transferred to the machine’s control system using a communication protocol developed specifically for this purpose, and prevent a tool crash with the component if the blade is retracted incorrectly
WGP Symposium on Production for Tomorrow
At the Production for Tomorrow Symposium hosted by the WGP (German Academic Society for Production Engineering), members provided insights into the challenges and opportunities of tomorrow’s production operations. The speakers, all of them themselves academics at universities and institutes, illuminated with their presentations how production technology in Germany is and will be addressing the sectoral trends involved.
In his keynote address, Prof. Eberhard Abele, the then President of the WGP and Director of the Institute for Production Management, Technology and Machine Tools (PTW) at Darmstadt University of Applied Science, dealt with the intermeshing trends featuring mechatronics, digitalisation, energy transformation, new production technologies and learning factories. For this purpose, he adduced impressive examples from specialisms of his colleagues at the WGP: intelligent sensor technologies for measuring and visualising machine loadings, simulation and optimisation of complex manufacturing processes, CAM systems in the cloud, consequences of the digital transformation and options provided by additive manufacturing. Prof. Hans-Christian Möhring from the Institute for Machine Tools (IfW) at Stuttgart University spotlighted in his presentation the possibilities opened up by intelligent machine components. For example, intelligent solutions for component clamping, designed to prevent component warping, and an adaptive process control capability for avoiding surface damage when milling complex parts, constitute the foundation for self-optimising production systems. Prof. Berend Denkena, the then Vice-President and current President of the WGP and Director of the Institute of Production Engineering and Machine Tools (IFW) at Hanover University, also addressed this issue, and presented solutions for extending the dynamic behaviour of machine tools and thus shifting the previous boundaries applying in the manufacturing process. Prof. Jan C. Aurich, who heads the Institute for Manufacturing Technology and Production Systems (FBK) at Kaiserslautern reported on performance-enhancing drilling tools featuring customised discharge openings and positions for cooling lubricants. Using modern-day methods for flow simulation (Computational-Fluid-Dynamics (CFD) Analysis), these discharge openings and positions can first be optimised by simulations and then validated in actual trials.
New Interface between Machine Tool and Cyber-Physical Add-On Modules
In particular, the Industry 4.0 Special Show offered exciting insights into tomorrow’s networked future for production technology. The academic community was represented at this special show by a large number of universities. One highlight was indubitably the government-subsidised BazMod research project, aimed at developing a manufacturer-independent standardised interface for exchanging media, data and energy between the machine tool and cyber-physical add-on modules. This enables an innovative functional expansion of machine tools to be achieved using sensor/actuator-based cyber-physical systems (CPSs), which had previously been integrated into the machine tool, depending on the manufacturer involved. Standardised contacts at the face expand the established hollow-shaft-cone holder and thus make possible an intelligent interface for supplying data and energy to intelligent tools. The signal transmission feature integrated into the spindle provides a link to the machine, thus rendering superfluous complex signal receivers that had hitherto been installed in the machining space at the tool-holder, and expanding the technical duty options for actuator-based tools.
Holistic Tool Management Systems
At EMO Hannover, in the context of Industry 4.0, holistic tool management systems were a major focus. Many manufacturers of high-precision tools such as the Iscar, Gühring and Sandvik companies as well as metrological specialists like Zoller from Pleidelsheim, supplied intelligent storage solutions for tools, components and accessories. Systems of this kind offer far more than merely an orderly and tidy tool management concept. The customer can precisely determine the tool costs per component, arrange for tools to be made available quickly and promptly, and avoid incorrect tool selection. In addition, intelligent systems feature a link to the machine tool, and receive information on a tool fracture, trigger a new purchase order at the tool vendor, and provide the machine’s operator with a constructionally identical tool. Systems of this kind render tool flows within the manufacturing operation and are clearer and more transparent.
With Digitalisation Initiatives to the Digital Factory
The machine tool manufacturer DMG Mori showcased numerous innovations at EMO Hannover 2017. One highlight announced was the open IIoT platform (Industrial Internet of Things) Adamos, which began operation on October 1, 2017 with 200 experts. It originated from the alliance between DMG Mori, Dürr, Software and Zeiss ASM PT, and is tasked with offering solutions for digitally networked production. In addition, DMG Mori uses Open Connectivity for access to its Celos-Ecosystem, so as to make possible a consistently harmonised digital data flow even with third-party makes or manual workplaces, thus taking one step further towards its vision of a digital factory. Besides innovative software solutions for networking, several new machine models were showcased: these included the even sturdier NHX 6300 horizontal machining centre for titanium machining, the high-dynamic-response DMU 200/340 gantry for machining large components, and the Multisprint 25/36 multi-spindle automatic lathes, which promise more productivity when machining long turned parts.
First Collection, Then Networking
Systems can be networked on different levels. The question here arises for machine tool users of whether all data must be sent to the cloud immediately. The answer to this is no, as far as Bosch Rexroth from Lohr am Main is concerned. The present-day net would certainly not be able to provide the capacity that would be necessary in order to transfer to the cloud the huge quantities of sensor information that machine tools are nowadays already able to make available. For this reason, Bosch Rexroth premiered at the EMO Hannover the Data Analytics Server on a machine from the machine tool manufacturer Pfiffner. What’s involved here is additional local computing power installed in the machine tool’s control cabinet, enabling machine and process data to be collected, stored and analysed. The aim is to process data beforehand, so as to admit to the cloud only the really essential compressed quantity of data, and in this way avoid overloading the data lines. It remains to be seen, though, what data it is expedient to send. They can, however, be determined by the users themselves using appropriate analytical tools and configuration programs that can be operated with minimal previous knowledge.
To enable machine tools to begin machining more quickly, Bosch Rexroth integrates measuring sensors and evaluation electronics into its linear guides, so that absolute position actual values can be acquired in real time and without a reference run. Positioning accuracy is further enhanced by means of another innovation premiered at the fair – an actively temperature-controllable guide rail. This newly developed feature is designed to avoid inaccuracies resulting from thermal expansion of the guide system.
Connected Machining – Networking Without the Cloud
Dr. Johannes Heidenhain from Traunreut demonstrated at EMO Hannover its Connected Machining function package, enabling consistently digitalised job management to be provided: transparent processes, time-saving work sequences and facilitated use of the data involved. The Remote Desktop Manager from Heidenhain premiered at the fair, for example, enables the customer to access the PCs located in the network and the software installed on them directly in the control system at the touch of a button. In the demonstration, Heidenhain did not restrict themselves to their own stand, but networked no fewer than 22 machines, which were distributed over the entire grounds of the fair. In order to check the status of the machines, there was no need to take a long walk over the huge exhibition grounds, since with the aid of the new StateMonitor software package a glance at the screen sufficed in order to find out the machine’s current state using RAG status displays. Further functions, such as displaying the current machining program or using filters so as to display only machines in a particular operating state, simplify the work of machine operators. Heidenhain wants to deploy the Connected Machining solutions in small and mid-tier companies with 10 to 15 machines. For this reason, they deliberately rejected the idea of a cloud solution and the concomitant risks, in regard to data security, for example. Instead, networking takes place on local servers
Digitalisation of Value Added Chain as Exemplified by a Drone Component
Siemens had already presented its concept for its Internet of Things (IoT) Ecosystem MindSphere as a digitalisation platform for all industrial sectors at the AMB 2016. MindSphere was demonstrated for the first time at EMO Hannover 2017. The application concerned involves digitalisation of the entire value added chain, as exemplified by an injection-moulded component for a drone. Machine tool manufacturers and operators were able, with the aid of such specific practical examples, to bring themselves up to speed on the advantages that the merging of the real and virtual worlds offers them. For this purpose, Siemens for EMO connected up more than 200 machines to MindSphere via the Manage MyMachine app. This enabled visitors to retrieve from a computer live information on the machining code being executed and the current operating state of machines from all over the world. Openness of this kind, of course, necessitates appropriate solutions with a view to data security. Identify3D is a security solution of this nature, which assures the traceability of digital manufacturing processes for protecting intellectual property while enabling the design and production data available to be used for components with technically precise specifications only for a limited quantity.
Besides networking solutions, Siemens also exhibited new software tools, such as Analyze MyWorkpiece. This easy-to-operate graphical tool enables the path of the tool’s tip to be visualised and analysed, so that different traversing speeds and tool orientations can be clearly edited and displayed. Only on this basis is it possible to detect errors and effect optimisations. The program operates irrespective of whether the machining code was created with the aid of any desired CAM software package or was programmed by hand.
On its stand at the fair, Siemens presented not only new software, but new hardware as well. Multi-touch displays have gained wide acceptance as an operator control concept, since the screens themselves work sturdily and dependably even in oily, dirty and harsh environments. For this reason, Siemens presented its new control panels in the 16:9 format and with multi-touch operator control. It can be safely assumed that panels of this kind will in future replace the old control consoles.
Vibrations at machine structures created during mechanical metalworking reduce the productivity of machine tools. In order to avoid this disadvantage, Siemens has developed an active damper. The designation of Active Vibration Absorber denotes a mechatronic system for machine tools that reduces vibrations at structures susceptible to them. This system, the size of a shoebox with a total mass of about 20 kg, is able to measure accelerations, and in variable-speed operation at frequencies of up to 200 Hz actively counter an oscillating mass of 10 kg.
Industry 4.0 Platform for Gear-Cutting
At EMO Hannover, the family firm Klingelnberg presented its Industry 4.0 solutional approach tailored to the gear-cutting industry, which is based on an IT platform. The key idea here is rigorous networking and holistic provision of process information along the entire process chain involved in gearwheel production. With this approach, the Hückeswagen-based company embraced the leitmotif of EMO Hannover 2017: Connecting systems for intelligent production. The resultant GearEngine IT platform constitutes the backbone of the cyber-physical Closed Loop production system. As a central link between the machine tools and other services (like the firm’s own SmartTooling tool identification system), it manages toothing data, production equipment, and the part history in three databases. For this purpose, the machines involved report to the platform individual data, e.g. about the tools and clamping devices used in machining the current gearwheel. This enables the entire production process for an individual gearwheel to be reconstructed. In addition, it is possible to intervene directly in the production operation, e.g. by improving the machining parameters between machining two gearwheels.
Expanded Service with Smartglasses within the Framework of Industry 4.0
Index-Werke and Hahn & Tessky from the Swabian town of Esslingen showcased various innovative solutions for the digital era within the context of its iX4.0 initiative. Besides a cloud-based IoT platform for receiving and editing machine and process data, the new service structure with smartglasses is particularly noteworthy. By using smartglasses with a real-time capability, the customer can repair his machine himself in the event of failures. A service technician from Esslingen offers visual support for this. The information and instructions are transmitted to the customer via the glasses onto his machine. This saves time and reduces standstills.
Integrated Sensor Technology for Avoiding Rejects
The Renishaw company from New Mills, UK, as a globally operating player in the field of high-precision technology, showcased its portfolio of systems for metrological applications and generative manufacturing. In the context of connectivity, Renishaw showcased an integrated metrological capability. In the shape of the Equator flexible test instrument, the firm offers an intelligent process control system that enables tool corrections in the CNC production process to be updated fully automatically. Thanks to direct embedding in the production operation, correction data are transferred from the measuring instrument to the machine, and taken into due account when manufacturing subsequent components. Waste can thus be simply avoided by continual re-adjustment.
Start-Ups in the Technological Environment
To enable large components to be flexibly and cost-efficiently machined irrespective of the component’s dimensions, the start-up Picum MT, created by the Institute of Production Engineering and Machine Tools (IFW) at Leibniz University in Hanover, is adopting fresh approaches. Instead of bringing the component to the machine tool, the Picum One, an intelligent tool robot weighing about a mere 100 kg with its own single-software solution and innovative metrology, is brought to the component. According to the start-up, procurement and operating costs are thus avoided, as are inaccuracies increasing with the machine’s size. The Picum system docks with any desired component, and automatically determines its position in the space to an accuracy of 15 µm. The prototype is fitted with five-axis kinematics and a 7.5-kW milling spindle, and handles tasks like drilling, milling and grinding. In future stages of development, expansions to the system will be able to perform additional jobs like measuring, laser-cutting, and 3D printing.
An innovation in the field of spindle manufacturing was showcased by Carbon-Drive from Darmstadt. The start-up venture from Darmstadt University of Applied Science is the world’s first manufacturer of full-carbon motor spindles for machine tool construction. High levels of specific rigidity and thermostability open up a multiplicity of advantages in the application concerned. Thanks to the reduced mass of the material used, the spindle is 50 per cent faster in all acceleration and deceleration functions, thus reducing energy consumption, non-productive times and costs. In particular, locally adaptable material properties are ideally suited for integrating metrological equipment to provide real-time monitoring of the metal-cutting process.
Summary
EMO Hannover 2017 showed that the radical shift towards digitalisation is being well received in the metalworking industry. Numerous IoT platforms like Adamos, Grob-Net 4 Industry or MindSphere were presented, which are progressing the advance of digitalisation. In line with this trend, manufacturers showcased numerous tools and other equipment that – fitted with sensors and digital communication interfaces – serve as suppliers of data to the digitally networked production systems. The up-to-the-future technologies nonetheless pursue traditional goals, such as trackable production processes, optimised resource utilisation, higher flexibility and increased productivity. The numerous new technological developments in machines, tools and machine components exhibited at EMO Hannover 2017, however, also contribute towards achieving these goals. In the field of additive manufacturing, particularly, there were many innovations on show – a fact that will indubitably favour a more cost-efficient deployment of the young technology.
Author: Johann Kiesner, Institute of Production Engineering and Machine Tools, Leibniz University in Hannover
Pictures: emo-hannover.de/en/news/media-library/impressions