Every machine tool is a complex construction carrying out the actual processing work by means of one or several tools
Whether it be in reshaping, punching, pressing or metal cutting – process monitoring is the key to optimized production. Process monitoring helps the worker in every phase: from the fitting of the machine to the observation of the production process to the quick stop in case of the threat of damage to the machine.
Every machine tool is a complex construction carrying out the actual processing work by means of one or several tools. In the end, the quality of the product is determined by the behavior of the tool and the workpiece. Any influencing quantities affecting the machine (or the process) will in the end be seen in the process quality. Thus, the process is affected by changes in the machines, in the tool, the environment (temperature), etc. Only if this process has defined courses, will the product quality meet the requirements. Intentional or accidental changes to these influencing quantities will have an effect on the process quality.
BRANKAMP process monitoring devices are fitted directly to the machine to record a process quality factor (PQ factor). This factor is displayed on the devices.
To monitor a process, certain limits need to be set, with the process monitoring device basically initiating a warning or a stop.
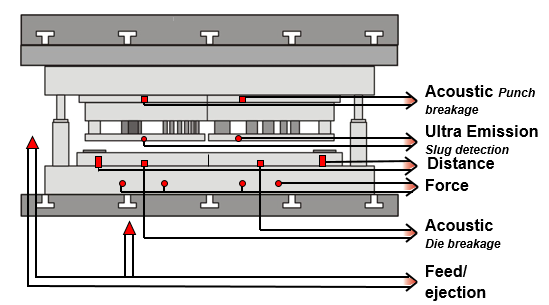
Process monitoring without sensor technology
The worker keeps an eye on the process according to his experience. In so doing, he visually observes the process. Due to his experience, he knows that he will be able to hear certain disruptions and, in the end, by measuring the workpieces, draw conclusions about deviations in the process. The more today’s machine tools are enclosed, the less he is able to watch or hear anything directly. He is therefore fully dependent on trouble signals or on the results of his measurements.
Process monitoring with BRANKAMP sensors
By means of sensor technology, recording the course of the process between the tool and the workpiece, the worker is able to watch the process purposefully. The relevant quantity will, in the following, be described as the PQ (process quality) factor. The more sensitive the sensor technology and the more intelligent the measuring parts are, the better and more ”accurate“ is the PQ factor.
In addition, the worker will, in the course of time, learn to assess the PQ factor correctly. The standard display shows the current process factor, the highest PQ factor thus far, and a limit set by him. He can then draw the appropriate conclusions from observing any changes and intervene or optimize.
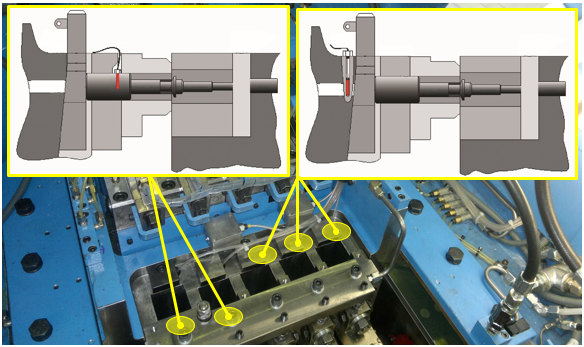
Displaying suitable factors for the process provides the worker with considerable advantages with respect to the optimization of the process and the ability to influence the costs. With the PQ factor, the worker, for the first time, has an objective measured variable by means of which he is able to assess the process quality.
Your benefits for implementing Process Monitoring:
- Machine and tool protection
- In-process quality control
- Increased productivity due to extended run-time, reduced downtime and stroke optimization
- Minimized tool and scrap costs
- Process optimization for more stable processes
- FactoryNet®4.0 interface to the MES / ERP interface
For more details, please contact:
Mr. Sarabjit Singh
Product Sales Manager – Machine Tool Solutions
Email: sarabjit.singh@in.marposs.com
Mobile: +91 9871900871
Website: www.marposs.com