Smart clamping and gripping – EMO 2019
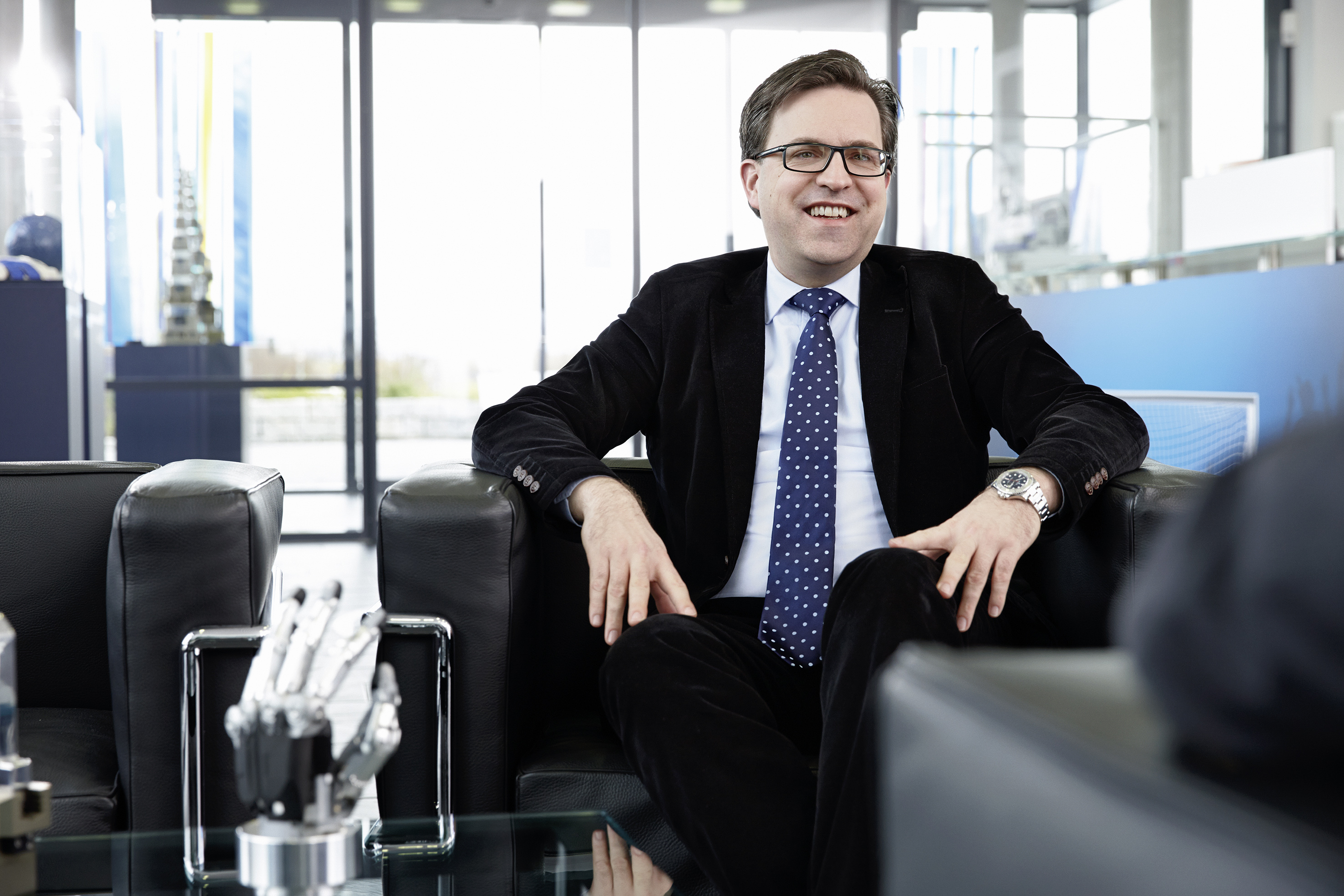
Chief Executive Officer
SCHUNK GmbH & Co. KG, Lauffen/Neckar, Germany
Photo: SCHUNK
Under the motto “Empowering Machines & Operators,” SCHUNK presented the smart future of gripping systems and clamping devices in modern production at EMO 2019. One thing is certain: The purely mechanical solutions of today will be smart tomorrow. Among the pioneers is the sensory toolholder iTENDO, the world’s first precision toolholder for real-time process monitoring and control for machine tools, which was honored with the MM award at the EMO. It can be used to detect vibrations, chatter marks, and tool failure, and adapt processes immediately and fully automatically. The sensory toolholder allows seamless documentation of process stability, real-time compatible control of RPM and feed rate, and unmanned limit value monitoring and tool breakage detection. SCHUNK demonstrated how this can be successful using practice-based pilot applications that provided some idea of the wide range of fields, in which the smart hydraulic expansion toolholder can be used. Applications range from classical milling applications and micro-cutting to deburring with brushes. Particularly in case of processes with severe fluctuations due to material or ambient conditions, in production of premium parts and processes with a high degree of tool wear, the iTENDO really comes into its own.
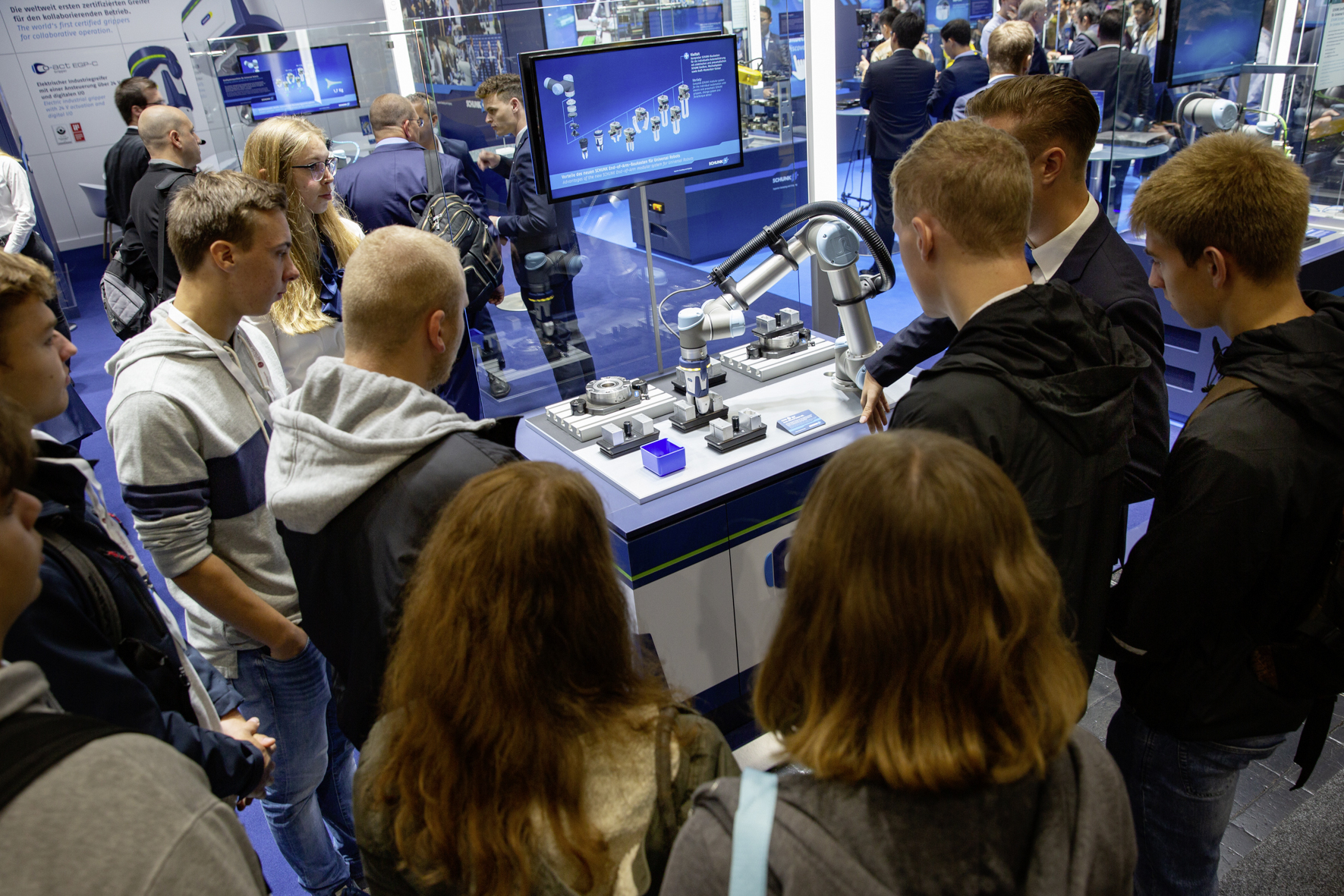
Photo: SCHUNK
Built-in intelligence
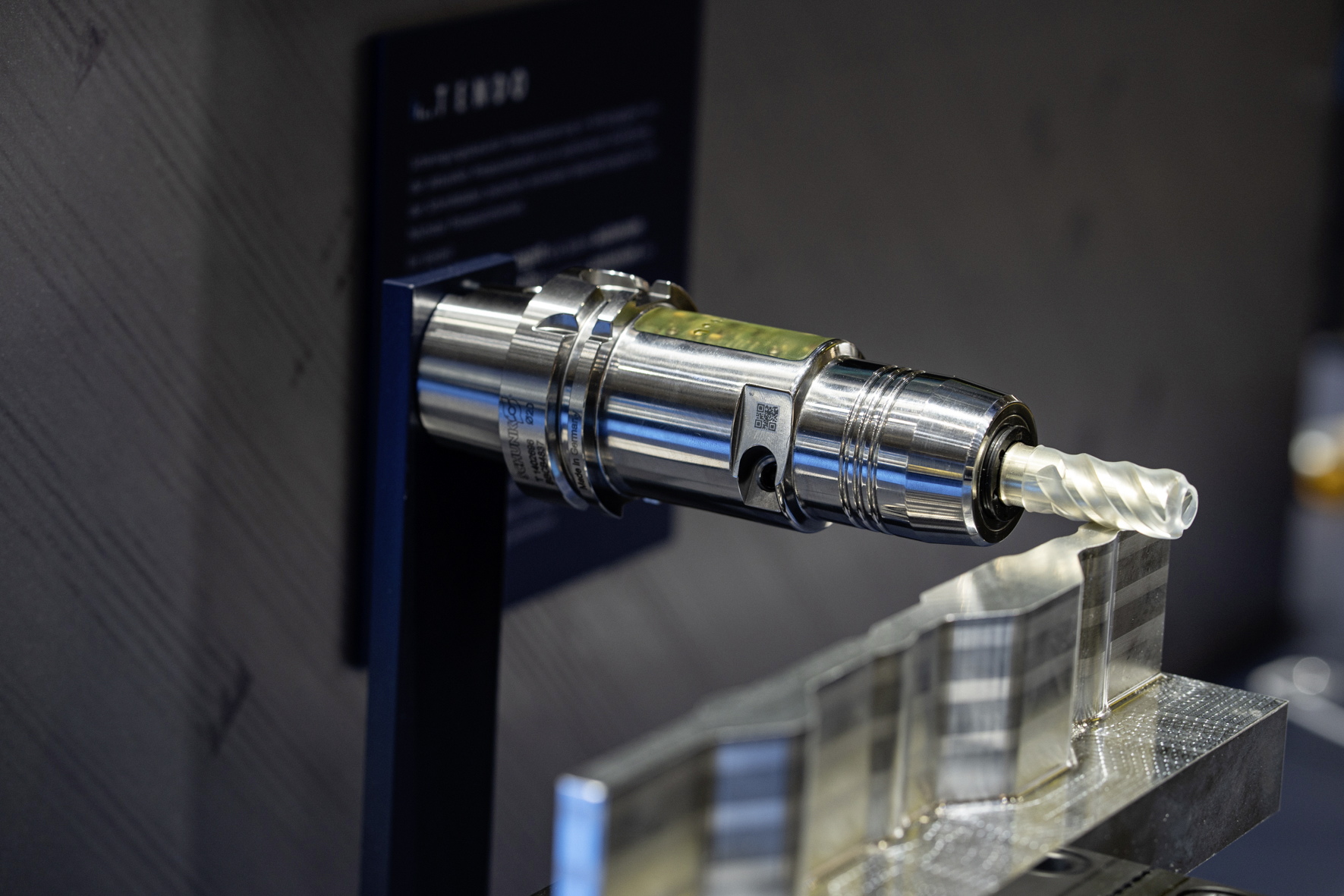
Further highlights were the sensory quick-change pallet module VERO-S NSE-S3, the smart long-stroke gripper EGL, presented for the first time with a plug-&-work-compatible interface for lightweight robots by Universal Robots, and automatable run-out and conical run-out compensation for high-precision workpiece clamping with tolerances of a few micrometers. In addition, SCHUNK presented a wide range of solutions for flexible, automated machine loading: Lean automation solutions, palletizing systems for the smallest batch sizes, but also high-performance Co-act solutions for human-robot collaboration. Chief Executive Officer Henrik A. Schunk is convinced that automated solutions in particular, will be of increasing importance in the years to come: “The boom in lightweight robotics, the growing demand in the area of human-robot collaboration, and the wave of automation among medium-sized businesses show that users are now focusing on automation of machine tools. At the same time, there is a clear demand for simplification. Gripping systems and clamping devices need to be commissioned rapidly and intuitively; and adapted simply and quickly to various part scopes.” With its extensive, highly compatible modular programs, SCHUNK is making an important contribution to ensuring that this becomes a success, adds the entrepreneur. schunk.com
A global first: The automatically adjustable run-out and conical run-out compensation based on hydraulic expansion technology is enabling a leap forward in terms of quality for high-precision workpiece clamping with tolerances of just a few micrometers. Photo: SCHUNK